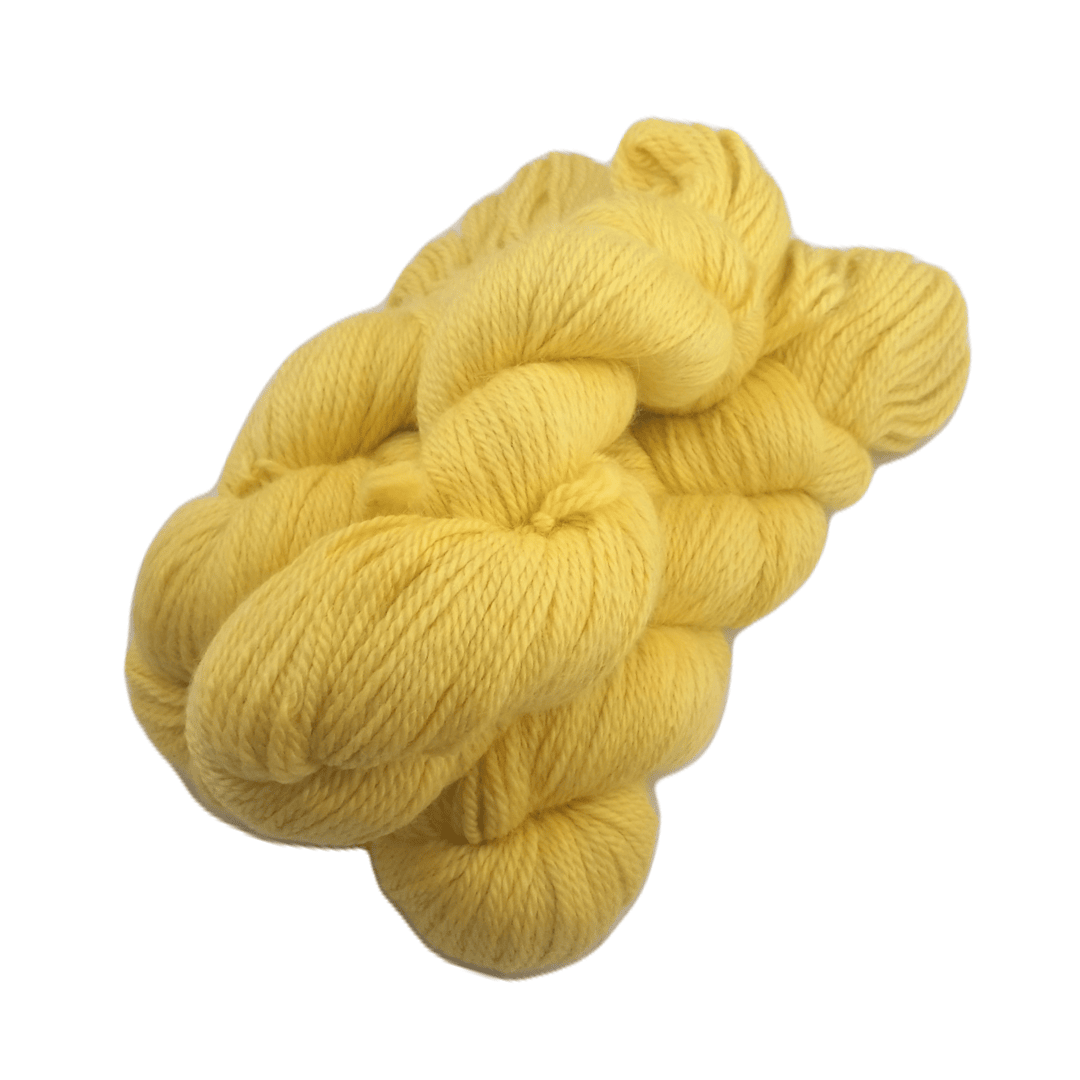
How Yarn Is Made: From Fiber to Fabric
Share
Yarn is the foundation of textile production, serving as an essential link between raw fibers and the fabrics we use in clothing, home textiles, and crafts.
While yarn may seem like a simple material, the process of transforming raw fibers into a usable form is both complex and fascinating. Different methods of yarn production result in varying textures, durability, and applications. In particular, the two primary methods—worsted and woolen spinning—produce distinctly different yarns that impact the final fabric's look, feel, and performance.
Cleaning and Carding
Before a skein of yarn can be spun, the raw fibers must be sourced and prepared. Natural fibers like wool, cotton, alpaca, and cashmere require shearing or harvesting, followed by cleaning to remove dirt, grease, and plant matter. Synthetic fibers, such as polyester and acrylic, are created through chemical processes and extruded into filaments that mimic natural fibers.
Once cleaned, the fibers undergo opening and blending. During this process, the fibers are loosened, fluffed, and mixed to achieve the desired consistency. Blending can combine different fiber types to enhance strength, elasticity, or softness.
Carding is a crucial process in yarn making, where fibers are passed through a series of fine-toothed rollers or brushes to separate and straighten them. This process removes impurities and creates a loose, airy sheet called a "web." The web is then drawn into long, soft strands known as "slivers." At this stage, the fiber preparation splits into two main pathways: worsted spinning and woolen spinning.
Worsted Yarn
Worsted yarn is known for its smoothness, strength, and durability. The process involves several meticulous steps to ensure the highest quality:
- Carding – The raw wool fibers are passed through a machine with wire rollers that align them in parallel while removing impurities.
- Combing – This crucial step removes shorter fibers (anything under a specific length) and further aligns the remaining long fibers, contributing to the smooth, uniform texture of worsted yarn.
- Spinning – The long, combed fibers are tightly spun, producing a strong, fine, and smooth yarn with minimal fuzziness or bulk.
- Finishing – Depending on the intended use, worsted yarn can be treated to add sheen or increase durability.
Characteristics of Worsted Yarn & Fabric:
- Smooth, strong, and less prone to pilling.
- Ideal for structured garments like suits, trousers, and fine-gauge knitwear.
- Has a firm, crisp drape that holds shape well.
Woolen Yarn
Woolen yarn is known for its softness, warmth, and lightweight nature. Its production follows a different pathway that retains shorter fibers and creates a loftier texture:
- Carding – Unlike worsted yarn, woolen yarn undergoes a gentler carding process where fibers are not strictly aligned. Instead, they are loosely arranged in different directions, which helps trap air.
- Omitting the Combing Stage – By skipping the combing step, shorter fibers remain in the blend, giving the final yarn a softer, more textured finish.
- Spinning – The loosely prepared fiber is spun with more air between strands, resulting in a fluffier, less dense yarn.
- Finishing – Woolen fabrics can be brushed or slightly fulled (lightly felted) to enhance their fuzzy texture and warmth.
Characteristics of Woolen Yarn & Fabric:
- Soft, lofty, and warmer due to trapped air.
- Has a more rustic or textured appearance.
- Ideal for cozy sweaters, scarves, and tweeds.
- Drape is softer but less structured than worsted fabrics.
Post-Spinning Treatment and Finishing
After the spinning process, yarn often undergoes a series of additional treatments designed to enhance its qualities and tailor it for specific applications.
For worsted yarns, common treatments include thoroughly washing the yarn to eliminate any remaining impurities, setting the twist to maintain a sleek and even texture, and applying chemical finishes that impart luster or durability. In the case of woolen yarns, treatments such as brushing and light fulling emphasize the yarn's naturally soft and textured appearance, while specialized dyeing processes ensure rich, even coloration.
Other techniques, like mercerization, boost fiber strength and enhance dye uptake, and anti-pilling treatments are sometimes applied to preserve the fabric's smooth look over time. The selection of these post-spinning treatments is carefully matched to the yarn’s intended use, balancing aesthetic qualities with functional performance.
From Fiber to Skein
Both types of skeins have their unique advantages depending on the desired application. Worsted yarns are better for tailored, structured pieces and garments worn against the skin, while woolen yarns are perfect for warm, insulating outer layers.
Ultimately, the art and science of yarn-making lies in the delicate balance of traditional fiber preparation, precise spinning techniques, and innovative finishing treatments. As modern technologies and sustainable practices continue to influence textile production, the journey from raw fiber to finished fabric remains a dynamic field—one where craftsmanship meets creativity to produce textiles that are both beautiful and functional for an ever-evolving market.